Home » Posts tagged 'concrete patios'
Tag Archives: concrete patios
How to Properly Repair and Maintain Concrete
Concrete damage can be addressed in a variety of ways. It’s important to take safety precautions, allocate enough time for meticulous assessment and precise execution, avoid common mistakes, and practice proper maintenance to ensure the longevity of a repair.
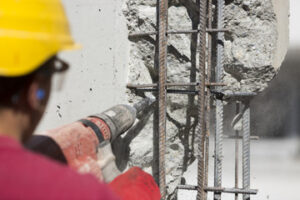
Structural repairs involve addressing cracks that impact the structural integrity of a concrete surface. Partial-depth repairs that abut working joints or cracks require a compressible insert to reform the joint or crack and keep the repair from bearing on existing concrete. Contact Concrete Repair Bismarck for professional help.
When it comes to crack repair, a few key points need to be kept in mind. First, the crack needs to be thoroughly cleaned. This step is important because leftover debris can compromise the effectiveness of the repair and cause new cracks to form. Using a wire brush and blower can help ensure that the crack is free of loose concrete or dirt. Once the crack is clean, it’s also important to make sure that the crack filler or patching product will be able to bond well with the existing concrete. This will allow for a long-lasting and durable solution.
Cracks in concrete are more than just unsightly; they can also pose serious safety hazards. For example, larger cracks can trip people and cause injury. While smaller cracks may catch high-heel shoes and cause them to slip or fall, repairing these cracks can minimize the risks of accidents and injuries. Cracks can also create moisture problems, allowing for moisture ingress that can damage the concrete and lead to structural issues. To avoid these issues, it’s important to repair concrete cracks as soon as possible.
It’s also important to distinguish between structural and non-structural cracks. Structural cracks are much wider, deeper, and more irregular in shape than non-structural cracks and can impact the stability and integrity of a structure. These types of cracks require immediate professional assessment and can be repaired with a variety of solutions, including polyurethane resins or foam injection.
Non-structural cracks are less severe and typically a result of poor construction practices or soil settlement beneath the concrete slab. These types of cracks can be repaired with a variety of products, including epoxy, polyurethane crack fillers, and water-based polyurethane caulks.
When repairing cracks in concrete, it’s often necessary to undercut the edges of the crack to create a more narrow base for the repair material. In addition, it’s often a good idea to use a backer rod when repairing deep cracks to help the filler hold its shape and prevent sinking. In some cases, it may be necessary to reapply the crack filler when it sinks or loses its shape.
Delamination
Concrete is a strong and durable material, but it can suffer from damage and deterioration over time. Fortunately, there are solutions that can restore damaged concrete surfaces and prevent future problems.
The first step in any successful concrete repair is proper preparation. This includes cleaning the existing surface and removing any dirt, debris or contamination. It is also important to make sure that the concrete patch will adhere properly to the existing surface. This can be achieved by using the right cement, sand and admixture mixture. Finally, it is critical to allow sufficient time for curing.
If the concrete patch is not properly prepared, or if the curing process is rushed, delamination may occur. Delamination is the separation of layers of concrete, usually caused by water or air that gets trapped under the surface of the concrete. This can lead to cracking, spalling and other damage to the concrete.
When a new slab of concrete is poured, it goes through a process called “bleeding.” This is when the solids in the concrete mix displace the water and air inside them. If the troweling process is started before this process is complete, water and air will get trapped under the surface of the concrete, creating voids that can weaken and break down the concrete over time.
Concrete repair techniques can be used to address delamination, such as stitching and epoxy injections. Stitching involves drilling holes on both sides of a crack and installing large staple-looking metal units into the hole to keep the crack from expanding. Epoxy injections are a more permanent solution and involve pumping epoxy into the crack to fill it.
Another common cause of delamination is poor construction practices. This can include skipping surface preparation, using the wrong products or rushing the curing process. It is essential that the concrete repair contractor has enough experience to understand these issues and follow the correct procedures to ensure a lasting solution.
While repairing old or damaged concrete can be challenging, it is possible to achieve good results. With proper care, the repaired concrete can last for decades and provide a strong foundation for other building materials.
Loose Slabs
Concrete slabs can sink, crack, or become unstable, which causes a number of warehouse issues. Slabs that sink are often caused by sub-slab voids, which occur in the soil beneath the slab. Fortunately, there are products and procedures that can address these voids and lift the concrete back to its original position.
Cracking is a natural part of the aging process in any type of construction material. However, this can cause structural damage that affects the integrity of the structure and reduces its lifespan. The causes of cracking in concrete are many and varied, ranging from temperature extremes that cause air pockets to expand or contract and shift the concrete, to soil changes that weaken the sub-base and compact it. The best method to correct cracking is to use a crack filler that will seal the concrete and prevent further damage, such as Quik Fix from Deco-Crete Supply.
Spalling is a common issue that can affect concrete slabs, particularly those with an exposed aggregate finish. The process causes the top layer of concrete to flake and break away, exposing the aggregate underneath. Spalling is usually a cosmetic issue, but can also be a safety hazard in high-traffic areas. The most common cause of spalling is moisture infiltration, which leads to expansion and contraction of the concrete and can also corrode the steel rebars within the slab.
Repairing a spalled or gouged surface requires removing the loose concrete and then cleaning the area to remove any debris that may have accumulated. It is important to isolate the deteriorated concrete from the surrounding slab and shoulder materials using full-depth saw cuts, which minimizes any damage that may be caused to the existing materials when the deteriorating section is removed.
If you are planning to repair a damaged concrete floor, consider the benefits of a precast floor system. This will not only save time and money, but it can also minimize the amount of disruption to your operations and increase your productivity during the installation process. A good precast system will include concrete slabs that are poured at the same time as the other slabs in the same area. This will reduce the time and labor involved, as well as help to ensure that the slabs are level and aligned properly.
Joints
Concrete slabs require joints to manage expansion, contraction and ground movement. They also control cracks by directing them in predetermined directions. The location and depth of these expansion and control joints is critical to the longevity of the concrete. They are especially important in large industrial structures like warehouses and distribution centers. A hard, uninterrupted concrete floor surface increases productivity and facilitates safe material handling.
However, over time and due to heavy traffic the joints can deteriorate. This is when we start to see visible cracks around the joint and/or water infiltration at the joint. A deteriorated joint filler can lead to loss of movement capacity which will eventually cause concrete damage.
Normally, the joints are filled with wood or a soft material called felt to allow the joint to move with thermal and ground settling changes without damaging the concrete. Unfortunately, these types of materials are prone to getting caught on equipment and pulled out of the concrete joint. Additionally, they don’t withstand the wear and tear of forklift traffic on the concrete.
For this reason, a newer, more compliant joint filler is required. We use a product called Trim-A-Slab, which is made from a rubber-like material that flexes and holds itself into the gap between concrete slabs. This allows the concrete to expand and contract as needed. It’s immune to rot, moves with the slab expansion and contraction, and doesn’t trap dirt and weeds like other less flexible products.
While control and expansion joints are vital to the long-term integrity of a concrete structure, they also contribute to its aesthetics. By strategically placing these joints, contractors can control the pattern of cracks that appear in the concrete and give it a more visually appealing look.
Concrete Repair – Improving Safety and Extending the Lifespan of Structures
Concrete is an extremely durable material, but it can be damaged by weathering and heavy use. Addressing this damage can improve safety and extend the lifespan of concrete structures.
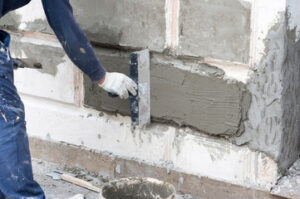
There are several methods for repairing concrete, depending on the extent and cause of the damage. Structural repairs are needed to repair cracks that impact the integrity of a concrete surface. Decorative repairs are needed to repair spalling and surface wear. Contact Concrete Repair Dallas for professional help.
Preparation of the existing concrete is a key step in any concrete repair. If the concrete is not prepared properly, it will not bond well to the new material. This will result in the repair failing quickly and costing more money. The preparation process removes all damaged and deteriorated concrete to make sure that the surface to which the repair will be applied is solid and sound. It will also remove any coatings, sealers, dirt, grease or oil that are on the surface of the concrete.
The prepared surface must be free from any water, salts, or chlorides that may damage the new coating, concrete repair materials, or even the concrete itself. This can be achieved by using a chemical treatment, or by removing the affected areas of concrete with a power grinder and then washing them down.
The concrete should be brought to a Saturated Surface Dry (SSD) condition after cleaning and profiling. This ensures that the repair material will not absorb water from the concrete, which could lead to poor adhesion and void formation. It also ensures that the new repair material contacts the existing concrete evenly and thoroughly, preventing weak spots or air pockets that can lead to premature failure.
Depending on the type of repair, the concrete may need to be prepared by mechanical means in order to open up the cracks for good adhesion. For example, epoxy injection can be used to repair cracks by welding them together, but this is only an effective method of repairing structurally weak concrete if the cracks are wide enough to allow water to flow through them.
All patch repair materials must be properly cured to develop a high-performance bond with the existing concrete. Curing can be shortened or skipped if workers are eager to finish the job, but this will ultimately reduce the life of the repairs and will require more time and expense in the future. Proper curing will also help the patch repair materials withstand exposure to weathering conditions and other service conditions. For example, a long moist curing period can slow down the loss of water from the repaired areas and prevent the surface from drying out and becoming de-bonding.
Repair Materials
A quality repair material is vital to the success of a concrete repair. The selection of a repair material requires consideration of its strength, durability, drying shrinkage, permeability, thermal expansion, elastic modulus and chemical properties as well as its cost. In addition, it must be compatible with the existing concrete.
Portland cement mortar and grout are the most common repair materials used to restore concrete structures. These repair materials are generally based on Portland cement and can be modified by the inclusion of blast furnace slag, fly ash or silica fume to improve their performance. However, the bond between these materials and the concrete substrate is poor. This incompatibility leads to stress concentration at the interface and debonding of the repaired area [62, 63].
Cracks are a natural feature of the aging process of concrete, and they can be structurally significant or not. The cracking is typically load-induced or related to intrinsic volume changes of the concrete such as drying shrinkage and thermal expansion. Cracking may also be caused by construction errors or other factors.
When selecting a repair material for repairing cracked concrete, consider the size of the crack, its location and whether it is active or dormant. For active cracks, a flexible repair material is recommended to allow for movement. Using a rigid repair material will usually result in the formation of new cracks at the interface of the old and repaired areas.
The choice of a repair material should also be based on the condition of the substrate to which it will be applied. For example, if the repaired surface will be subjected to cold weather, the repair material should be able to withstand low temperatures and freeze-thaw cycles. It should also be durable against chemicals and abrasion.
Research has shown that the surface roughness of the substrate plays an important role in the shear bond strength between the repair material and the existing concrete. Various surface preparation techniques can be applied to roughen the existing concrete to enhance the shear bond strength, such as mechanical grinding and shotblasting. However, sandblasting was found to be the most effective method of increasing the shear bond strength, probably because it creates an uneven surface which increases the mechanical interlock of the repair material with the substrate.
Applying the Repair
Concrete repair is an essential part of the process of maintaining a building or structure. It is the process of restoring deteriorated concrete to its original condition by filling in damaged areas with a repair material. The resulting repair can be either cosmetic or structural. It can restore the appearance of a structure to its original state, or it can repair a structural defect, such as a crack, by adding strength to a weak area.
The first step in repairing concrete is to assess the extent of the damage and determine what type of repair is required. This will be determined by the function of the concrete structure and will range from cosmetic to structural reinstatement. The underlying substrate will also be a factor in this determination. In addition, the type of repair will be affected by environmental factors such as dimensional characteristics (drying shrinkage), thermal coefficients and freeze/thaw resistance.
Once the concrete has been identified as requiring a repair, it is necessary to clean the surface to remove dust, debris, oils and existing paint. This is important because the repair material will not adhere properly to a dirty or contaminated substrate. Physical methods such as sand blasting, grinding or pressure washing can be used for this purpose. The surface of the concrete should then be profiled to create a roughened texture to improve the mechanical bond between the repair material and the existing concrete.
This will help to prevent the repair material from penetrating into the existing concrete and causing further deterioration. Once the concrete is cleaned and profiled it should be brought to a “Saturated Surface Dry” (SSD) condition. This is important because the dry concrete will rob water from the new repair material, which could result in an improper curing and a weak bond.
The final preparation that must be made is to mark the area to be repaired. This will help to ensure that the correct amount of repair material is applied, and it will also reduce debonding around edges. A hammer and chisel can be used to cut away the concrete from the damaged area, or for larger areas a power saw with a diamond blade might be required.
Post-Repair Maintenance
Concrete surfaces are exposed to heavy loads and weathering on a daily basis, leading to natural wear and tear. The deterioration of these structures can lead to structural damage, a loss of safety and visual appeal, and increased maintenance costs. In order to maintain the durability and visual appeal of these surfaces, it is crucial that they are properly maintained with high-quality repair products and proper application techniques.
There are a wide variety of repair methods available to address the different types of damage in concrete surfaces. The method chosen should be appropriate to the type of damage being addressed. For example, using surface repairs for structural cracks can compromise the strength of the concrete.
Identifying the cause of the damage is also essential. There are several common types of concrete damage, including plastic-shrinkage cracks, hairline cracks, and surface spalling. Plastic-shrinkage cracks are small and short in length and appear in the concrete as it is curing. They typically form due to the settling of the concrete or changes in the surrounding environment.
Hairline cracks are shallow and thin in width and tend to be more widespread than plastic-shrinkage cracks. They are often caused by natural settling and can become larger over time. Surface spalling is the result of the deterioration of the concrete’s outer layer. It can occur in a single area or throughout the entire structure.
Crack fillers are an effective solution for cracks that are minor in size but can exacerbate into more extensive problems if left unattended. These crack fillers contain a liquid formula that binds to the cracked concrete to restore its structural integrity.
Epoxy resin injections are another effective repair solution for concrete surfaces. These injections use a two-part epoxy that bonds to the crack surfaces to bring them together. Lastly, polyurethane foam injections are a great option for fixing voids and holes in concrete. This material is injected through ports in the damaged concrete and expands to fill the voids.
No matter what type of concrete surface you need to repair, it is important to follow these tips to ensure that the process goes smoothly and the results are successful. By taking the necessary precautions, hiring professional help when needed, utilizing high-quality repair products, and practicing regular maintenance practices, it is easy to keep your concrete looking beautiful for years to come.