Home » Posts tagged 'printing'
Tag Archives: printing
Advantages of 3D Printing
3D Printing Phoenix AZ, is a radically different manufacturing method that builds parts layer by layer. It has some distinct advantages over traditional processes.
In an era that thirsts for innovation, knowing how 3D printing works is important. This innovative technology allows businesses to bring ideas to life swiftly, ushering in a new era of customization.
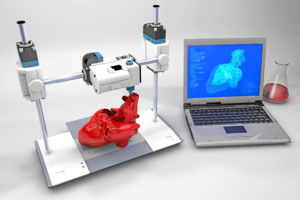
As the name suggests, rapid prototyping quickly turns designs into physical models using 3D printers. With the limited visual communication afforded by computer renderings, this allows designers to communicate with colleagues, clients, and collaborators in impossible ways. As a result, it reduces the time and cost of design and development.
Conventionally, it could take months or years to build a product prototype. However, with 3D printing technology, it can be done in hours. This helps reduce the number of iterations needed to get the final product right, cutting development costs and saving the company money.
While traditional processes like injection molding require a lot of upfront capital and setup, 3D printing allows for low-cost, quick iteration to test different variations of a product. With this, engineers can evaluate a product’s fit, function and form and make changes before investing in production. It also enables them to create high-fidelity prototypes that look and work as if they were final products, and guides the product through a series of validation stages toward mass production.
In addition to being faster and cheaper than traditional methods, the digital nature of 3D printing can be integrated into business models. This makes it easier for firms to move sideways and upstream, for example by outsourcing manufacturing. Alternatively, they can cut out intermediaries and sell directly to customers.
The key to successful product development is getting user feedback and incorporating it into the design process. For this reason, it’s important to include users in the early stages of testing and prototyping. This can be as simple as sharing prototypes with a small group of users or letting them try out a finished product before it’s released. For example, Freetrade had a waiting list of 20,000 users before their app was officially launched on the App Store.
The ability to iterate quickly and inexpensively through the use of rapid prototyping allows companies to minimize costs, resulting in a smaller risk when bringing new products to market. This translates to lower startup costs and more revenue potential. It also ensures that the product meets user needs and adds value, increasing the likelihood of success.
Rapid Manufacturing
As the 3D printing industry matures, its focus has shifted from rapid prototyping to rapid manufacturing. The latter focuses on the use of additive technologies to produce functional prototypes and end-use parts. This approach is highly valuable to product companies that wish to avoid high upfront costs of traditional fabrication, long lead times for procuring new molds, and the waste associated with outsourced machining or injection molding services.
The rapid manufacturing process utilizes digital files and software automation to transform CAD models into real-world products, often in just hours or days. These models can be tested, evaluated and iterated to optimize designs for performance, cost and weight. This allows product developers to bring better, more useful and more durable products to market faster than ever before.
Once a final design has been approved, the file is sent to the 3D printer. The machine then builds up the physical prototype layer by layer using a variety of materials such as plastic, metal and ceramics. The printed prototype is then subjected to a number of post-processing steps to refine its appearance and functionality. The results of this testing and iteration can be used to improve the initial product concept.
The speed of the process enables designers to quickly go from ideation to finished product and eliminates costly delays. This is especially valuable for smaller companies that lack the capital or time to invest in large-scale production and large inventories of end-use parts.
For example, Melbourne-based company Quad Lock created a vibration-dampening smartphone mount for motorbikes with 3D printing technology, and were able to create and test 100 iterations of the part in just one day.
Regardless of whether a product will eventually be produced with traditional processes such as injection molding, or by other additive manufacturing methods, it’s important to ensure that prototypes are built with the final manufacturing method in mind. This will help to prevent mistakes and errors that can be costly during serial production. For example, if the end-use product will be made with a hard, durable material like steel or aluminium, then the prototypes should be printed in these materials.
Additive Manufacturing
Additive manufacturing refers to the use of 3D printers and related technologies to create physical models based on computer-generated designs. The printing process works in layers, constructing the model piece by piece from the bottom up. The model then undergoes post-processing and finishing steps that produce improved dimensional accuracy and surface finish.
As of 2017, domestic 3D printers are becoming popular, especially with maker/enthusiast/early adopter communities. They can produce functional items, such as backscratchers, door knobs and other household objects. They can also make artistic items, such as ornamental figurines.
In addition, the technology is starting to be used for end-use manufacturing, in particular, for metals. The technology enables speedier production of metal components than can be achieved with conventional techniques.
Despite this, the industry has yet to experience significant growth in end-use applications. This is in part because of the difficulty of overcoming the cost barrier to adoption and use. The price of the machines is still much higher than that of traditional production equipment, and the cost of the materials needed to make end-use prints is often prohibitive.
One of the main obstacles to end-use use is that printing a complex, durable object can take a long time, even with additive processes. It can take a few hours to construct a single, small model with contemporary methods, but several days for larger and more complex ones.
3D printing technologies are evolving quickly to support newer materials, as well as a wider range of shapes and sizes. For example, the latest polymer-based printers can print in multiple colors, and they can also construct multi-material objects. Some of these newer machines can print a mixture of plastics and metal, or a combination of polymers and ceramics. In the case of metal additive printing (also known as direct metal deposition or DMD), the printer apparatus consists of a nozzle that deposits molten metal onto a surface, which is then solidified by an energy source such as an electron beam or laser. This is similar to the way in which a metal casting machine operates.
Customization
Customization refers to tailoring a product or service to meet the needs and preferences of specific customers. This may involve adding a company logo or personalizing a physical object to make it unique and more appealing. In manufacturing, customization can help to reduce production costs and shorten lead times. 3D printing is an ideal tool for customization because it enables the creation of a variety of products that can be made to order, reducing the need for extensive inventory or production delays.
Many industries have begun to use 3D printing for customization. The medical sector, for example, uses SLA to produce customized medical devices, such as hearing aids and dental implants, that are matched to the patient’s anatomy. In consumer electronics, 3D printing is used to create customized accessories such as phone cases, earbuds, and gaming controllers that reflect the individual’s style and personality. The rail industry also utilizes 3D printing to create bespoke parts, such as arm rests for drivers and housing covers for train couplings.
In the home, 3D printing has become popular for customizing furniture, ornamental objects, and other household items. Off-the-shelf printers are capable of printing a wide range of materials, including plastics and metals. Many consumers choose to purchase home 3D printers to save money and avoid paying retail prices for custom-made items.
Despite the increased popularity of DIY 3D printers, they are not without their limitations. Many off-the-shelf machines cannot produce certain geometries and details, as well as require time and effort to fine-tune print settings. Additionally, some printed results can vary slightly from a customer’s initial expectations due to design constraints and mechanical properties such as the need for support structures in complex designs.
Nevertheless, the technology is evolving rapidly. In fact, 79% of respondents to TWI’s recent survey reported that they expect their companies to increase their adoption of 3D printing for mass customization in the next three to five years. This will enable them to achieve nimble supply chains, improve product quality, and deliver products and services that truly meet consumers’ requirements. In addition, 3D printing will improve supply chain resilience by enabling manufacturers to produce parts locally, reduce inventory, and print on demand.